Liquid Screed Services:
Liquid screeding is a popular method in modern flooring, known for creating smooth, level surfaces that are ideal for various types of flooring installations, especially underfloor heating. Despite its benefits, tackling liquid screeding has unique challenges that make it more difficult to handle than traditional sand-cement screeds. Here’s an in-depth look into Liquid Screed Hampshire, which can be hard to manage, and the key factors contributing to its complexities.
Specialised Equipment and Expertise Requirements
One of the primary reasons liquid screeding is challenging is that it requires specialised equipment and skilled labour, unlike traditional screeding, which can often be done with basic tools like a trowel and level. Liquid screeding demands specialised pumps, mixers, and levelling devices.
Because liquid screed is self-levelling, it must be applied controlled to ensure it spreads evenly, often necessitating a trained team to manage the process efficiently. Unskilled handling can lead to uneven surfaces, cracks, and other defects that undermine the quality and longevity of the floor.
Precise Preparation and Cleanliness of the Surface
Surface preparation is critical with liquid screeding and must be executed with precision. The subfloor must be meticulously cleaned and free of dust, debris, or any substances that could affect the adhesion and levelling of the screed.
A primer ensures proper bonding between the subfloor and the screed. Even a small oversight in preparation can result in issues like poor bonding, delamination, and inconsistent thickness, leading to costly repairs.
Time-Sensitive Application Process
Liquid screeding is time-sensitive because it has a limited working time after mixing. Once prepared, the liquid screed begins to set quickly, so it must be poured and levelled efficiently. Any delay during the pouring process can lead to an uneven surface, cracks, or other defects. In larger spaces.
The entire area must be screeded within a specific timeframe to avoid cold joints (where one section of screed begins to set before another is applied), which can cause structural weaknesses. Therefore, liquid screeding requires a carefully planned approach, making it more challenging than traditional screeds, often allowing for a more relaxed pace.
Temperature and Humidity Control
Temperature and humidity significantly impact liquid screeding, affecting the drying and curing. Extreme temperatures, especially high heat, can accelerate the setting time, leading to improper levelling or cracking. Conversely, cold temperatures can delay curing, increasing the risk of moisture-related issues like mould growth or weak bonding.
Humidity control is also critical, as excess moisture in the air can slow down drying, while very dry conditions may cause premature curing, leading to surface cracks.
Tackling these environmental variables requires careful monitoring and adjustment, often needing specialised knowledge and equipment, which adds to the complexity of liquid screeding.
Moisture Testing and Extended Drying Times
Liquid screeding involves more intensive drying and curing times compared to traditional screeds. Though liquid screeds dry faster to the touch, they retain moisture longer, especially when installed over large areas or in thicker layers. Before installing any flooring over the screed, it’s essential to conduct moisture testing to ensure it has reached an acceptable dryness level.
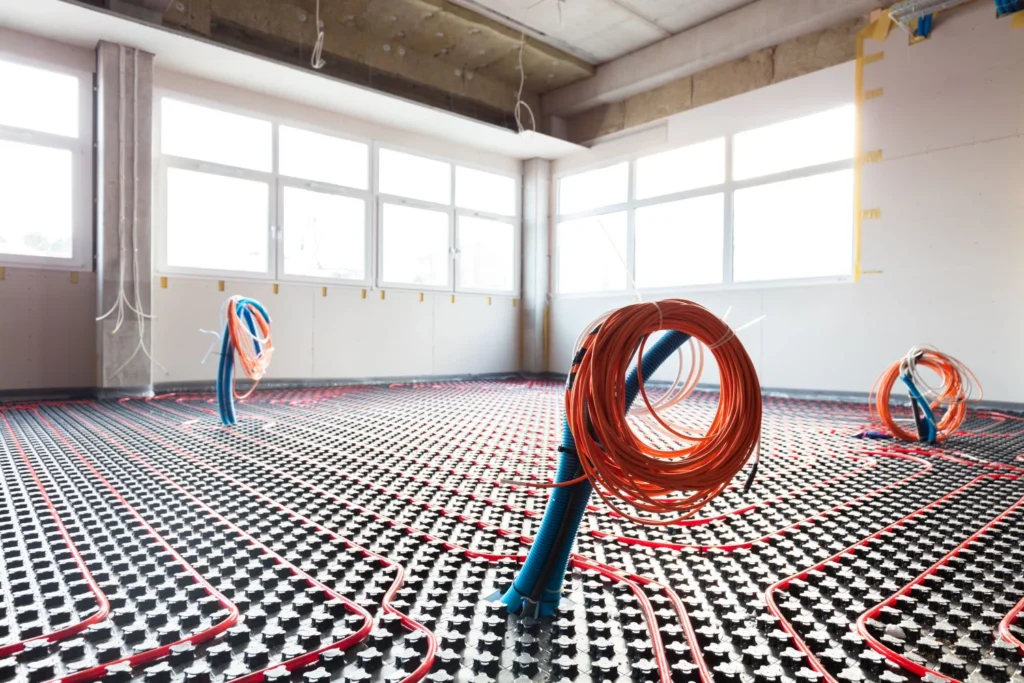
Failure to properly test and allow sufficient drying time can damage floors, especially moisture-sensitive floorings like hardwood. This aspect demands patience, precise timing, and equipment, which can complicate project timelines.
Risk of Cracking and Shrinkage
Liquid screed is prone to cracking and shrinkage, especially if not installed correctly or if the curing process is not adequately managed. The screed can shrink as it dries, creating surface cracks that affect the floor’s appearance and structural integrity.
To combat this, installers often incorporate additives like fibres or anti-cracking agents, but even with these precautions, there’s still a risk if the process isn’t managed precisely. This sensitivity to cracking and shrinkage requires experienced installers who understand how to minimise these risks, making the process harder than traditional screeding.
Higher Costs and Project Planning Challenges
Liquid screeding is typically more expensive than traditional screeds due to the need for specialised equipment, skilled labour, and additional preparation steps. The installation cost can increase significantly if unexpected challenges arise, such as environmental factors or substrate issues.
Furthermore, project planning can be challenging due to the need for precise timing, environmental control, and extended drying periods, which can delay other aspects of the construction project if not carefully managed.
Conclusion:
Tackling Liquid Screed Winchester is more complex than it may initially seem. The process requires specialised equipment, skilled labour, precise planning, and careful attention to environmental factors, among other considerations.
Properly managing these difficulties involves knowledge, experience, and planning, making it challenging for many builders and homeowners. However, liquid screeding can create a durable, efficient, and visually pleasing floor surface with the right team and preparation.